Analyse - Reliability Centred Maintenance / FMEA
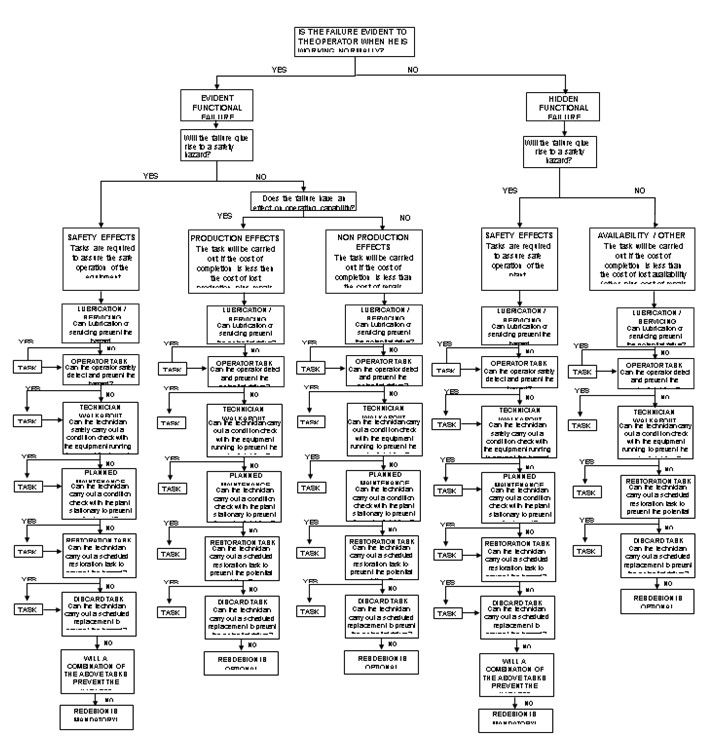
Zero Carbon Engineering started working with RCM/FMEA and setting up maintenance systems in 1996 after training as a coach with South African Breweries. Since then the managing director has led implementations for several large FMCG companies and on a smaller scale in retail.
Failure Mode and Effect Analysis was initially developed by two aviation engineers - Nowlan and Heap. In the 1960's the incident of accidents associated with jet aircraft was unacceptably high. Studies proved that the fundamental assumption of that every major component in the airplane (such as its engines) had a specific "lifetime" of reliable service, after which it had to be replaced (or overhauled) in order to prevent failures—was wrong in nearly every specific example in a complex modern jet airliner. In fact they discovered that many of the failures were triggered by the maintenance interventions themselves.
The US Department of Defense sponsored the authoring of both a textbook and an evaluation report on Reliability-Centered Maintenance, both published in 1978. It was quickly picked up by the aviation industry and military with significant improvements in reliability.
The diagram to the right is a version of MSG3 (maintenance steering group 3) and is a logic chart that allows the project team member to work out the appropiate maintenanc routine for a given piece of equipment.
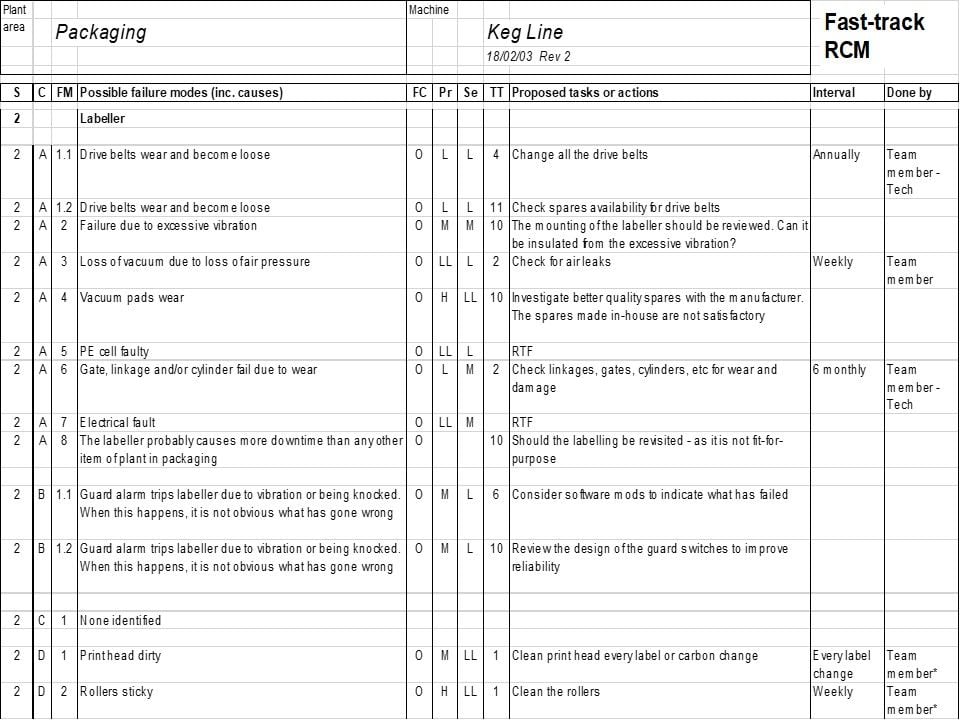
The FMEA process produces a table as shown left, where a machine is broken down into assemblies and then the known failures are broken down to cause (FC), priority (Pr), severity (Se) and task type (TT). The maintenance task is then described, along with frequency and who is required to do it.
On some tasks it is identified that failure is completely random, whereby the maintence task is shown as RTF (or run to failure) and the task is to make sure appropriate spares are available.
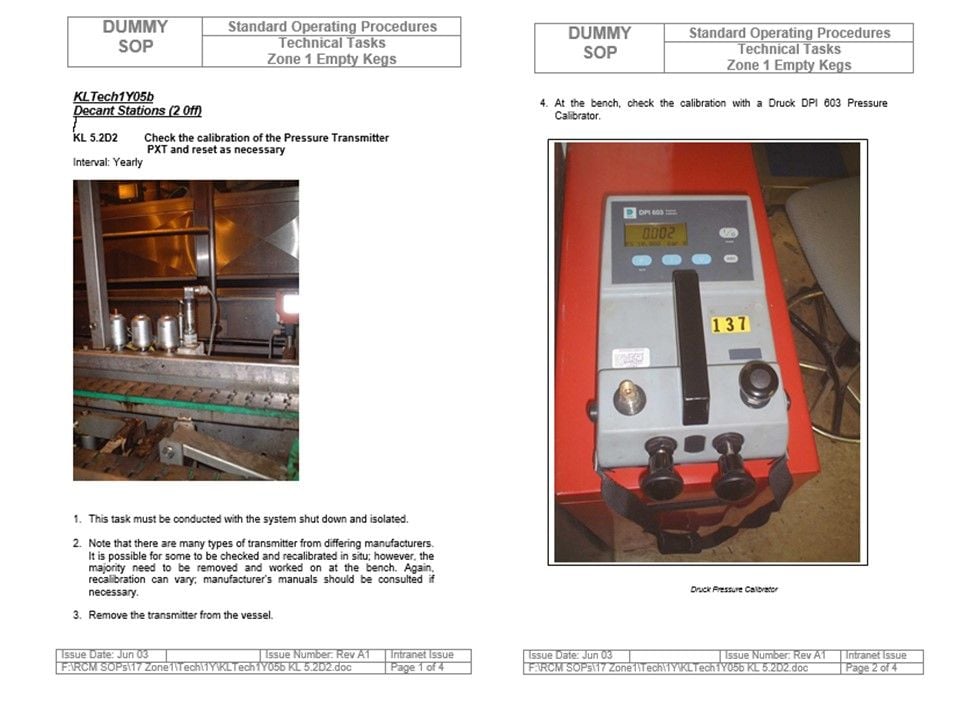
Once the analysis is complete, standard operating procedures both for maintenance and operations that are easy to follow with the minimum of training are produced (as per image right), team members are trained to carry out the tasks, the strategy for spares (order in, hold bonded spares, hold in stores etc) is decided, and the task is loaded onto the PPM schedule of the sites maintenance system.
As a control, completion of maintenance tasks, spot audits and checking of KPI’s such as Overall Equipment Effectiveness or ratios of planned / unplanned maintenance are then carried out.
The general experience of implementing this sort of system is an increase in productivity and a reduction in maintenance costs.