Case Study - FMCG Site Energy Project
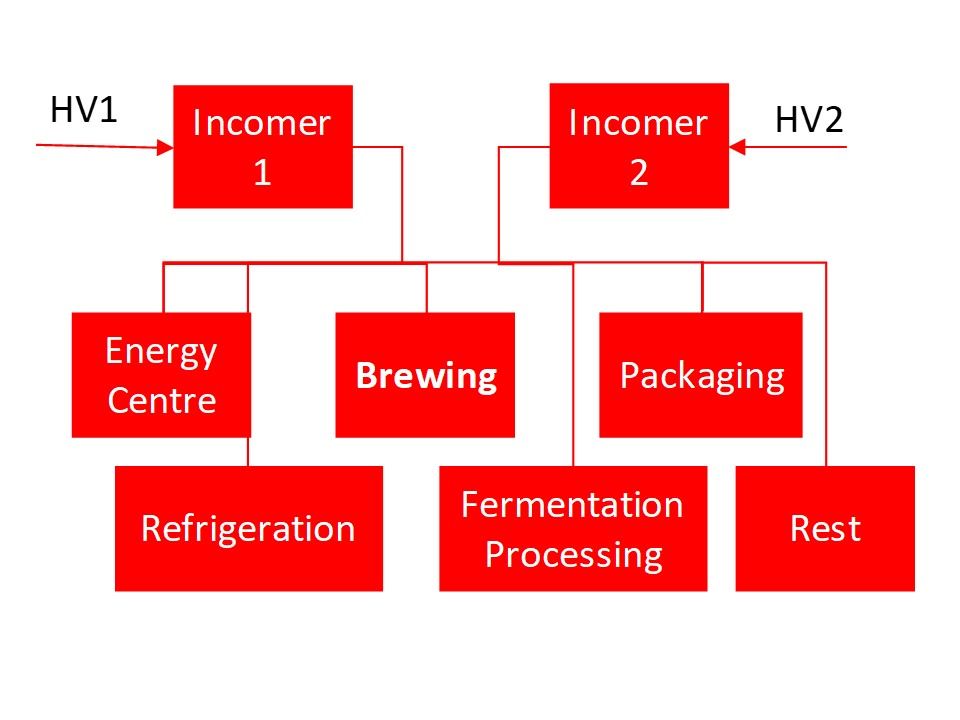
A long established production site was reviewed as it had a number of issues relating to old utilities plant on site. The site was using 25GWh (c £2.7m) of electricity and 42GWh of fuel (oil and coal - £1.0m). Compared to its peers the site was inefficient both from an energy budget and carbon viewpoint.
The site was fed mains electrically through 2 x 11kVolt incoming mains connected to six 11kvolt to 400Volt transformers around the site (see diagram right). Most of the electrical distribution equipment around the site was relatively new and in good condition.
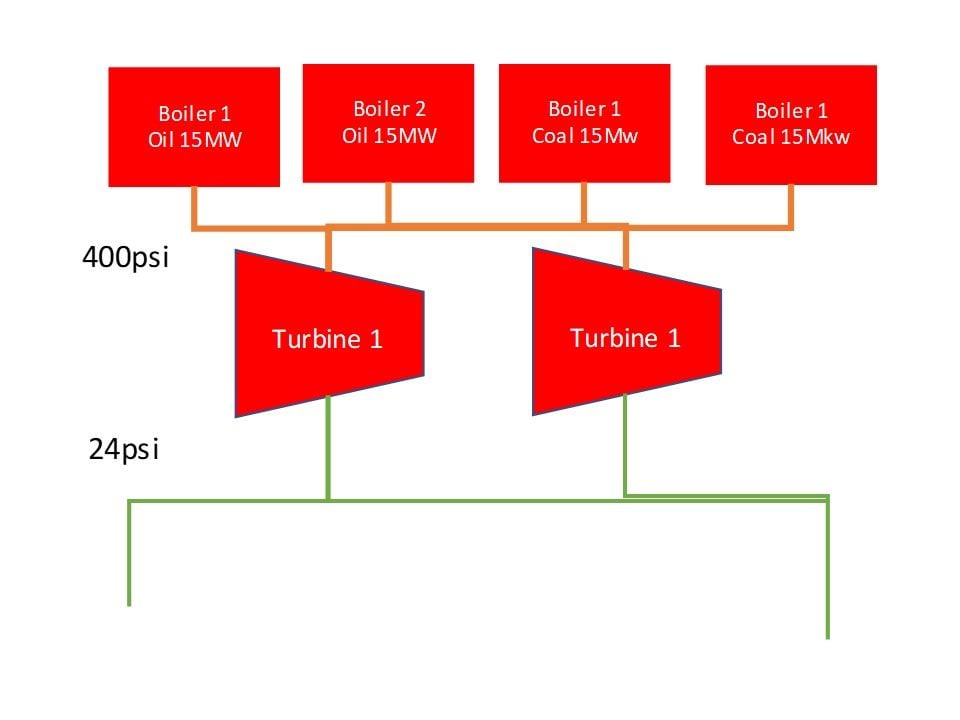
The site had 2 x 25 ton (15MW) coal fired boilers and 2 x 25 ton oil fired boilers. These raised steam at 400psi and fed through 2 steam turbines to feed the site with electricity and heat (steam at 24psi).
The turbines were in a dilapidated state and had not run for some time. The boiler and turbine arrangement were also expensive to maintain and unreliable. The incumbent energy centre operations contractor had tabled a proposal to install a 600kWe gas fired CHP with waste heat boiler.
High level modelling indicated that it was of borderline performance under DEFRA guidance.
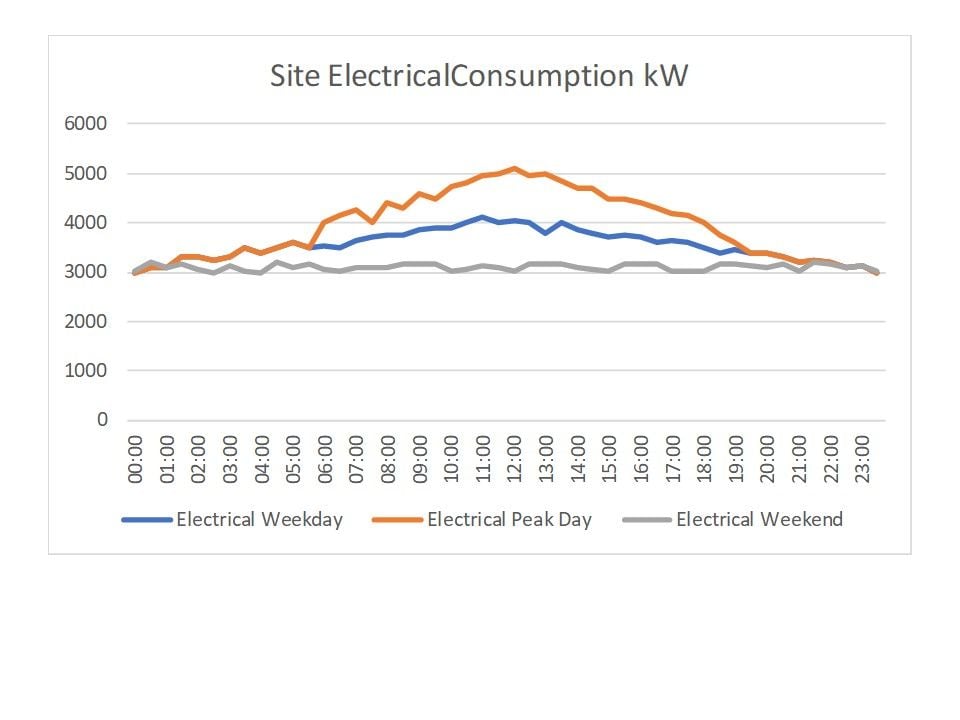
The site electrical demand had a fairly predicatable pattern with scale only changing between weekday and weekend with some seasonality (see peak day).
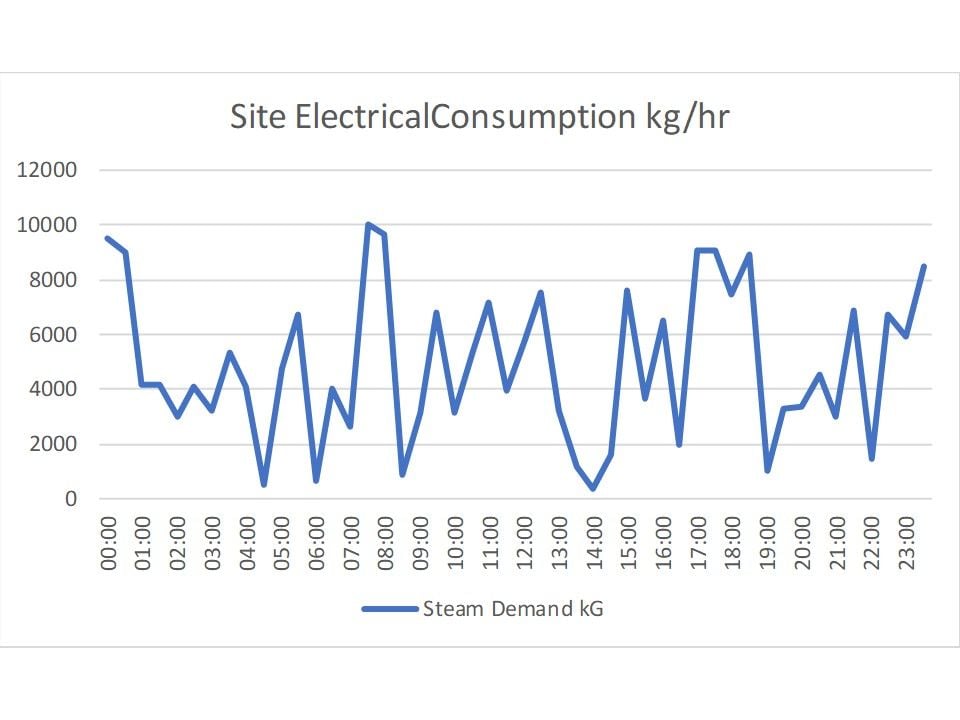
However heat demand was far more unpredictable with significant swings around a base load of 3000kg/hr between 10,000kg/hr and zero kg/hr,
A CHP can only run down to 50% of full load and operate comfortably and does not like following rapidly swinging loads. Modelling on what a CHP was capable of demonstrated that it would end up dumping 20% of all heat raised as it would be unable to dynamically follow the load.
To see if it was necessary to allow the process loads to impact the energy centre like this, a surplusing valve was installed. This protected the energy centre by only allowing the steam flow to increase at a controlled rate and by protecting the upstream pressure. Having installed the valve there was no impact on process operations at all. With the steam load damped, it was demonstrated that the site could cope with 2 x 12 Ton gas fired boilers.
Rerunning the CHP model with much lower steam loads proved that it wasn't viable in terms of payback.
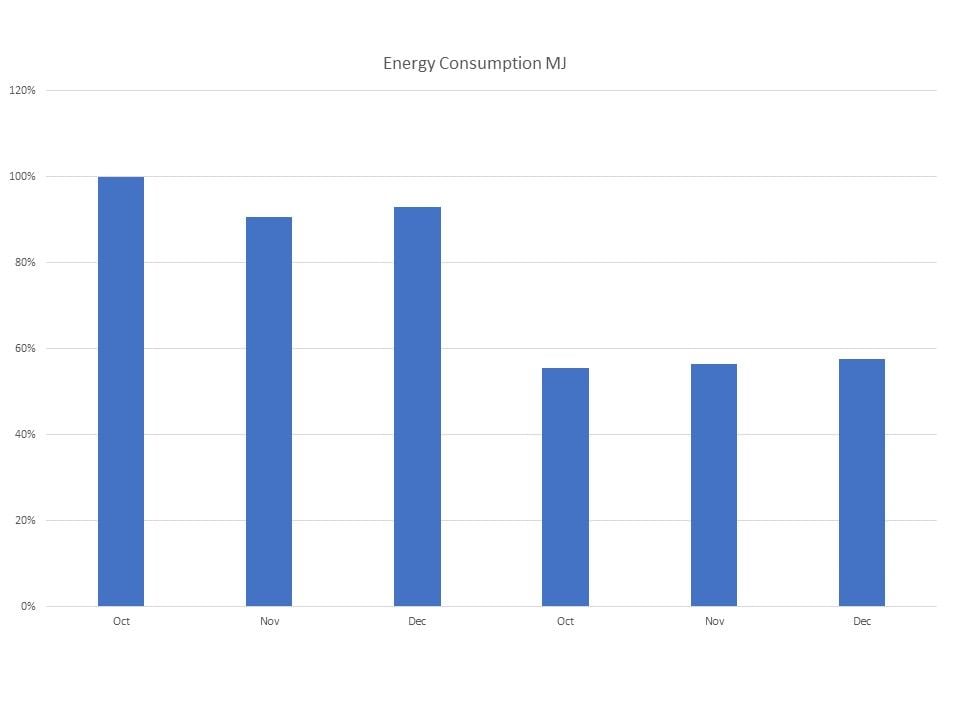
The change in boilers brought about a 40% reduction in energy consumption and 80% in Carbon by changing fuel. (graph right shows Oct-Dec year before and year after).
There was also a significant saving in water consumption (not venting 20% steam any more) and maintenance and manning (far less reactive and breakdown activity).
The overall payback was 18 months.